フロンメタルSの軸受特性
1.摩擦係数
乾燥すべり面ではTFE(テフロン)が流動し、一部相手面にも移着してなじみ面を作ります。
従って処女面の摩擦係数(μ)は0.1ですが、すべり開始と共に徐々に減少して0.05~0.1の範囲に入ります。
2.耐摩耗性
(a) 乾燥すべりの場合(フロンメタルS)
a-1 ●材質的特徴
フロンメタルSの表面には摩擦中にTFE(テフロン)の潤滑性流動層が形成されます。また相手面にも移着して同様な被膜層が形成されてなじみ面となります。
フロンメタルSの摩耗粉事態も潤滑性を有していて、たとえ摩耗粉となっていてもこれが摩耗を促進することなく、その面に居残ったものはあらためて流動していずれかの面に移着しています。
このような現象は素地を作るポリイミドが熱硬化性であること、摩耗粉が化学変化しにくいことによって得られた非常に好ましい軸受すべり面の性質で、フロンメタルSの特長です。
a-2 ●スライダーベヤリング(Sの被膜同志ですべる軸受)
Sの被膜はすべり摩擦中に相手面に移着してなじみ現象を呈しますが、最初から軸受と相手面の両方にSの被膜をコーティングしておけば、最初からなじんだ状態ですべり、 摩擦現象が起こらないことがわかりました。
この理由は両方のTFE(テフロン)の潤滑性表面層の間には凝着現業はあっても凝着力が小さいこと、またSの被膜同志の接触では硬さも強さもほぼ同等であり、しかも合成樹脂であるため多少の弾性があるので、相互に食い込み、押し込みの作用が小さく、いわゆるアブレージョン(機械的破壊摩耗)が起きにくいことに由ります。
しかし厚膜で高荷重(100kg/cm2以上)になるとこの相互の食い込みがひどくなり、かえって逆効果になることがあります。 このような場合はむしろ薄膜同志の組み合わせがよくて、200kg/cm2以下で実用的です。
このように同材質同志で組み合わせた軸受をスライダーベヤリングと呼びます。これは耐熱性で熱硬化性樹脂であるポリイミド樹脂のみに得られる性能です。
この形式は軸受と軸、ピストンとシリンダーなどに応用されます。
また、ころがり軸受と同様の寸法形式で実用されます。
a-3 ●摩耗係数
合成樹脂の摩耗量を示す式として一般に
W=KPVT・・・・・・(A)
が利用されます。ここにWは摩耗量(cm)、Pは荷重(kg/cm2)、Vはすべり速度(m/sec)、Tは時間(hr)、Kは摩耗係数(cm3、sec/kg・m、hr)です。
これはWがPVに比例し得る範囲内で成立するものですが、便宜的に利用します。
(A)式でK は小さい方が摩耗は少なく、フロンメタルSは0.1×10-6以下になります。(第5表参照)
今、PV値=10kg/cm2・m/secで使用する場合、0.05mm(0.005cm)摩耗するに要する時間は
K=0.1×10-6 で T=5000
K=0.05×10-6 で T=10000
K=0.01×10-6 で T=50000
となり、フロンメタルSの寿命は5000時間、スライダーベヤリングでは1万時間という実績値が出ています。
第3図は実験による摩耗量との関係を示したものです。
A曲線はS被膜と相手は焼入鋼、B曲線はS被膜同志で摩擦させたものです。
Aの方は大体10時間位でなじみ面となり、その後の摩耗量は少ないが微増します。
Bの方は最初から摩耗は進まず、なじみということもないようです。なじむためには相手面に極めて少量でも移着しますが、この移着量は膜の厚さ、P、Vによって変化します。
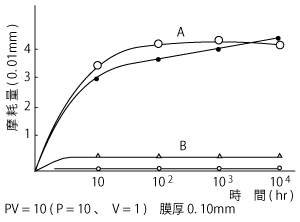
a-4 ●膜厚と摩耗との関係
膜厚は薄い方が摩擦抵抗は強くなります。これは金属台金の強さ、硬さの影響が出てくるからです。従って膜が厚いことは必ずしも寿命の長いことと一致しません。一度なじみ面になればその後の摩耗進行程度は薄い方が少ない傾向にあります。
第4図は膜厚と摩耗量との関係を示します。
薄膜0.05mmの場合は0.02mm位は相手に移着するため早く摩耗しますが、その後の進行は極めて少なく、摩耗量はほとんど一定です。これに反して厚膜0.2mmになると、100時間かかって0.05mm摩耗してなじみ面となり、その後は大体一定になります。
膜の厚い方が全体的に見ればそれだけ寿命は長いのですが、0.2mm以上は熱放散性が悪くなり、摩擦温度上昇度も大きくなりますので原則としてフロンメタルSの厚膜の方も0.10~0.15mmにしたわけです。
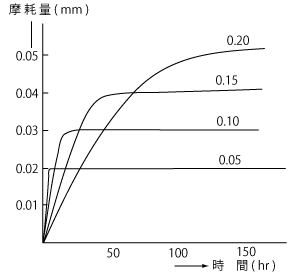
このように熱放散性と耐摩耗性ならびに膜の破断強さと密着強さの関係で0.10~0.15mmを適正値としましたので、皆様の設計やコーティング御依頼の台金の寸法は是非この厚さになるよう御指定下さいますよう御願いします。
a-5 ●相手面の仕上げあらさと摩耗
相手面の仕上げあらさが大きいと何時までもヤスリで摩耗させているようにアブレージョンが絶えません。 やはり仕上げ面は良好の方が移着膜の密着も強いし、早く移着を完了してなじみ面となります。
しかし鏡面にする必要はありません。第5図は軸の仕上げあらさと負荷能力P(kg/cm2)との関係を示したものです。図中Bはバフィング仕上げです。すべり速度(V)が大きくなるに従ってあらさの影響も大きくなります。Vが著しく小さくなれば、あらさは問題にしなくてもよいようになります。
薄膜の場合は特に仕上げもよくし、ステンレス、クロームメッキはなじみ性も少し劣るので、すべり条件も小さくする方が安全です。
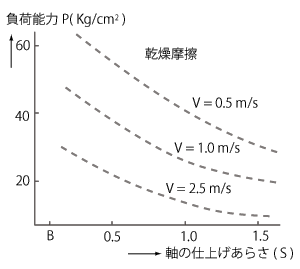
a-6 ●PV値
PV値は仕事量ですから、これと摩擦熱とは密接に関係します。
すなわち、乾燥摩擦面の温度Tは
T=C・1/K1 ・1/K2 ・μ・P・V・・・・・・(B)
で示されます。
Cは常数、K1は軸及びハウジングを含む機械の熱放散度、K2は軸受自体の熱放散度、μは摩擦係数、Pは荷重、Vはすべり速度です。
合成樹脂では軟化点、溶融点、流動点などによって耐熱限度は略一定しています。そのため、耐熱性の良い材料ほどPV値は多くなります。
今Tを一定とすると、K1とK2の大きいもの、μの小さいものはPV値は多くなり、使用機械の熱放散性の良否すなわち厳寒の冬と酷暑の夏、加熱機械と冷却機械、小さい機器と大きい機械の一部ではそれぞれPV値に当然差が生じます。
また、合成樹脂層を金属表面に薄くコーティングしたフロンメタルのPV値が合成樹脂単体のものに比較して多いことも主として熱放散性によります。
従って膜の薄いものが案外寿命があることもわかります。フロンメタルSは熱硬化性樹脂であるポリイミドが膜の構成結合体となり、これにTFE(テフロン)が潤滑剤として分散している形式の組織ですから、膜としての軟化点、融点はなく、(B)式でTは大きくとれます。
第4表に最大PV値と、PとVのそれぞれの許容値を示してあります。フロンメタルSの被膜の耐圧強度は2000kg/cm2なので、Vが小さくなればPは2000kg/cm2までとることができるようになります。高温軸受として使用する場合、その周囲温度は軸受すべり面で生ずる摩擦熱による温度上昇と共に加算されてるので、PV値は周囲温度が高くなるに従って小さくすべきです。
フロンメタルSの実用的最高周囲温度は350℃と考えます。
約300℃の乾燥炉中の軸受のPV値は7以下で現在実用されています。
a-7 ●黒鉛摺動体の相手面としてのS
黒鉛摺動体とフロンメタルSとは相互に円滑な滑りをします。通常はSの面を黒鉛が動いて摩擦すべりをする場合が多いのですが、逆にSの方が摺動面となり、黒鉛の方が静止する場合も実用されます。現用のものはいずれも往復すべりです。
黒鉛は硬質な方が成績はよろしい、軟質では逆効果の出た例があります。このすべり面では相互に摩耗粉が発生せず、Sの面に僅少移着した黒鉛とSとの混合面が黒鉛と接触すべりをしています。
黒鉛と金属との接触すべりでは摩擦熱の発生も多く、摩擦係数の変化も大きいので、とかく故障が起こりやすいのですが、Sコーティングした面では長時間円滑な滑りを持続します。
(b) 油膜潤滑の場合(フロンメタルS)
フロンメタルSの被膜は油が滲みていれば、合金軸受の給油状態とほぼ同程度のすべり性能を示します。 被膜はなじみ性がよくて、耐摩耗性も優秀なため、またさらに化学的に安定なために、油が汚濁されないし、焼付現象はありません。 しかし、被膜の密着力は合金軸受に比較して小さいために衝撃性高速高荷重用には不適です。
第6図と第7図は油を使用した場合の比較試験結果で、ホワイトメタル(WJI)とKJ3(ケルメット、銅-鉛合金)とフロンメタルDとの試験片の温度上昇を示したものです。曲線が水平であることは温度が一定であることであり、すべり面での変化がなくなじみ性がよく摩耗もしていないことを示します。
また第8図は、油中摩擦の比較摩耗量(各荷重60時間運転)を示します。
WJ1はホワイトメタル1種、LBC3は鉛青銅3種、FMBはフロンメタルB(現在廃止)
、FMDはフロンメタルD、FMSはフロンメタルSです。
フロンメタルDはポリカーボネートと4弗化エチレンとの混成物被膜を0.20mmの厚さに、フロンメタルSはポリイミドと4弗化エチレンとの混成物被膜を0.15mmの厚さにつけたものです。ポリカーボネートの融点は230℃でホワイトメタルと同一です。
ポリイミドは熱硬化性で軟化点、融点はなく、350℃までは強度を有し、ケルメットと大体似た耐熱性を有しています。
このような耐熱性合成樹脂の被膜を金属台金に薄膜にコーティングしたSは、熱伝導性も合金軸受と何等変わらないことは当然考えられます。実用的には油が汚れない、摩耗しない、焼付現象がないなどの特性を活用する使い方が賢明で、条件も合金軸受の基準で中速中荷重位が限度です。
また、クロームメッキの代わりにSがよく使われています。また、フロンメタルDはコーティング後、微量のパラフィンを含滲させますが、実用時でもさらに少量の油かグリースの補給があれば著しく耐久性があります。
(C) 防錆、防蝕、離型性(フロンメタルS(黒色))
フロンメタルS(黒色)は優秀な防錆、防蝕力を有しています。被膜の厚さは0.05mmまでの薄膜です。
0.1mmまではできますが、0.03~0.05mmが通常です。
被膜は組成的には1層から3層で構成され、少々摩擦しても金属地が露出するようなことはまずありません。
また耐酸性、耐アルカリ性は優秀で、単なる防錆、防蝕に利用するには品質過剰気味ですが、酸洗機、各種コンプレッサーの内張ライニングに実用されて好評を得ています。
被膜との密着性は鋼が最高ですが、鋳鉄、ステンレス、アルミニウム合金のどんな形状物でも、その任意の場所にコーティングできます。離型性では接着剤処理機器、ゴム成形金型、食品、薬品用機器など用途は無限です。